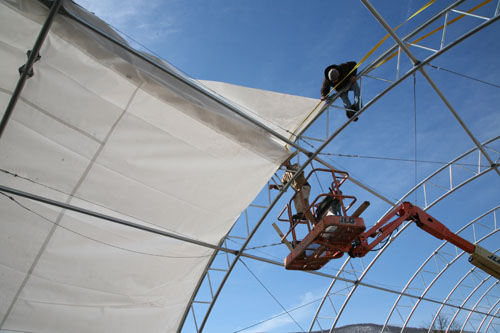
Our co-workers in the Catskills have been as busy as bees! They have just finished building a new ClearSpan building to store our JOHNHOUSHMAND reclaimed wood slabs. A year ago, a snowfall of an impressive 54 inches caused the roof of one of our smaller slab storage units to collapse. Our entire slab inventory, which consists of thousands, needed to be combined into one cramped center with slab piles stacked at nearly 8 to 10 feet high!
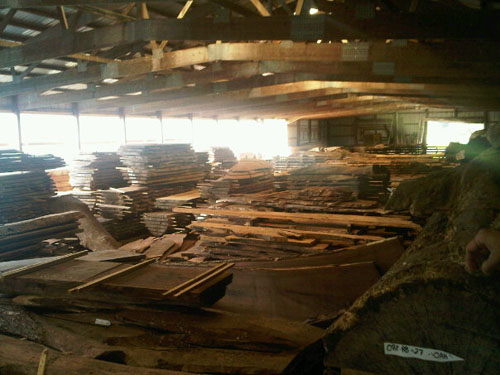
This new building will almost double the storage space we currently have, with an additional benefit: to air-dry slabs in order to shorten kiln-drying time. During a Catskills summer, the heat from the sun on the fabric roof of the building combined with the breeze from open doors allows the slabs to dry quickly yet evenly. We are thrilled that this process will reduce the energy needed to make our beautiful tables, thus making an organic product even greener!
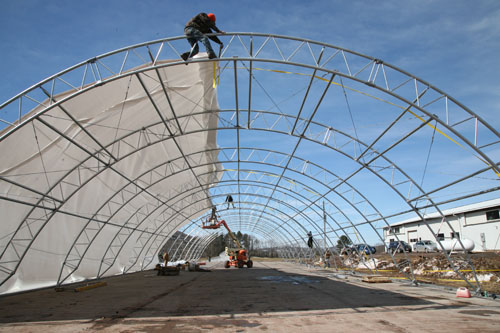
The ClearSpan building is made of galvanized steel frames and a fabric roofing cover. It measures 195 feet long, 55 feet wide, and 22 feet high. Definitely a great sized space to comfortably house our precious organic slabs!
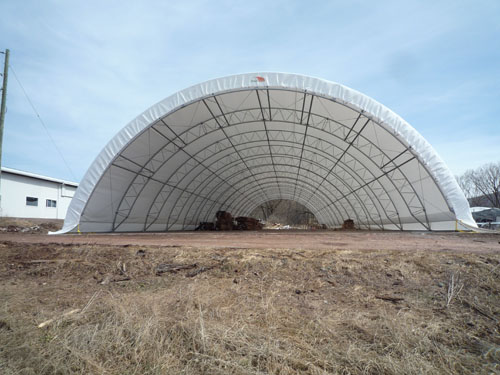
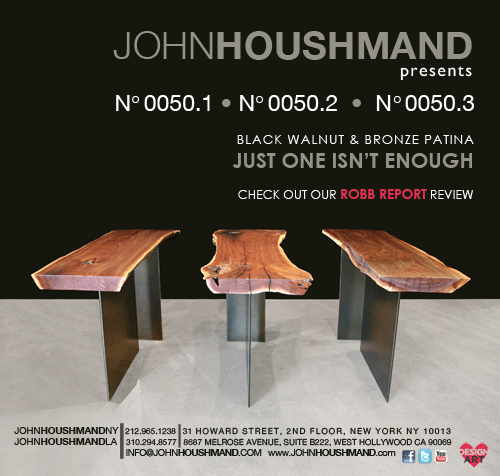
Variations within individual wood logs are such that different segments will show a wide range of personality. These three console tables, No. 0050.1, No. 0050.2, and No. 0050.3 each have their own distinctive flavor. The black walnut tops were crafted from squared off roundbacks and are in line with JOHNHOUSHMAND‘s philosophy of using the entire tree. A pair of perpendicular bronze patina legs were then attached to complete each piece.
These three consoles are being sent off to the Hyatt Regency Atlanta (covered previously on this blog) where they will be used in hallways and entryways. These consoles would translate perfectly to the home: in a foyer collecting car keys and mail, a unique sidebar set-up at a cocktail party, or showcasing family photos and keepsakes behind a couch.
Though no matter the use it is clear, repetition of this kind is far from boring. One just isn’t enough!
The industrial process of harvesting trees for wood products has become such a specialized method that only a very small percentage of trees are deemed usable. They must fit into a matrix that includes such considerations as log size, hardness, color and grain structure and aesthetics, mill-ability, weight, and more. As most wood products are now engineered, the logs must be veneer-capable…in other words they must fit on a rotary or sequential slicer that filets or ribbons off the log a cardboard-thin skin capable of being handled by specific machinery, means, and methods.
As such, anything too large, irregular, crotched, unique, and different cannot pass through the industrial process. What IS used is a banal cartoon of the world of wood…perfectly straight grain, homogenized, devoid of knots, inclusions, imperfections. Although they intend to be prime grade A materials, they actually lack all the visual character and information that is the birthright of a real tree. That world includes a visual, informational, and vibratory history of all aspects of a tree’s life, including its species characteristics as well as its individual lifetime, where it lived, climate, soil, sunlight, water conditions, historical events, traumas, boom times and more…the “terroir” of a tree.
Trees that are not compliant with the industry’s tooling and marketing demands are more often than not destined for land fill and firewood. Shocking to consider that a 250 year old hardwood sage would be cut into firewood rather than carefully milled out and allowed to tell its story. And to remind humanity that wood does NOT look like wallpaper, but rather a map of time, life, existence, and the unique trajectory of witnessing and participating in reality.
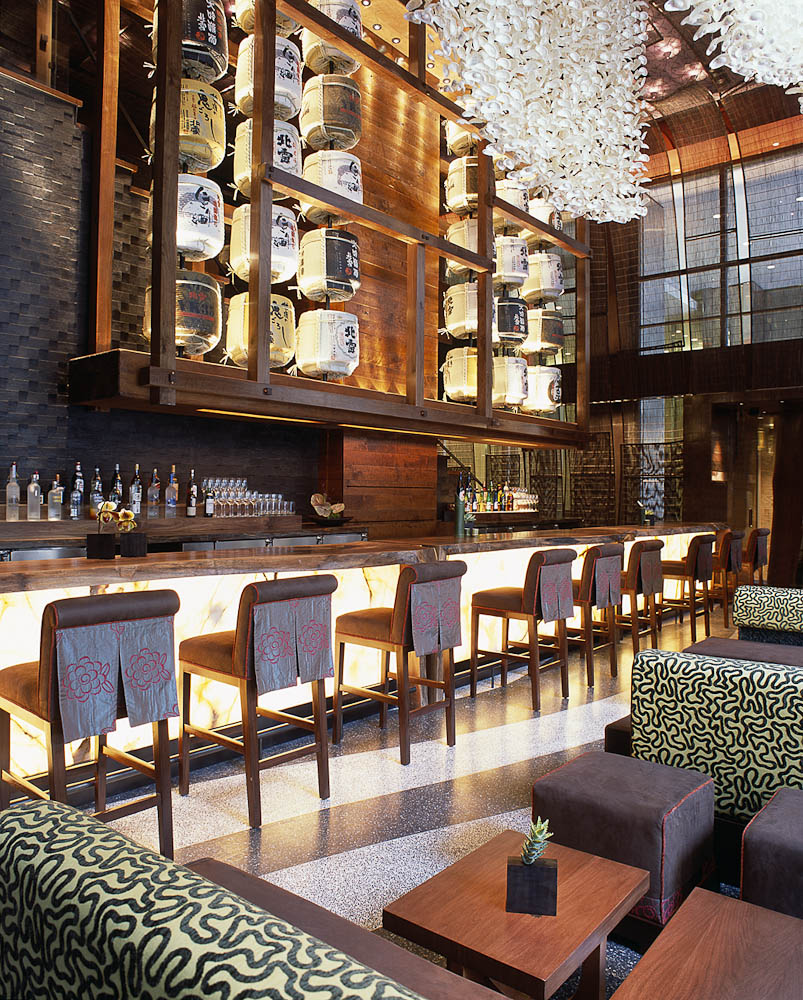
The new Nobu restaurant on 57th St. in New York
The Nobu project was originated in the design world of the Rockwell Group, with an intention to bring the beauty and soul of wood into this very specific urban space. Of course the influence of Japanese aesthetics and their affection for wood was a paramount piece of the paradigm. From the slab wood and glass door nestled in a portal of black walnut “timbers,” to the natural edge wood bars and their complement of back-lit onyx panels, the entire project required a sculptor’s hand on the wood combined with an extraordinary degree of technical ability never before attempted.
The timbers – large and small – had to actually be made as hollow assemblies owing to the need to place lighting, air conditioning, and wiring within. End-grain pieces ranging in size from 6″x6″ to 24″ x 36″ were cut and super dried by microwave, and then laminated onto stable substrates to eliminate cracking and degrade failure. These end grain plugs were then deftly mounted in the hollow “timbers” which were then assembled into portals and towers. The glass door was made by radically reinventing the door-making process. We started by scuttling the engineers’ design of a steel frame with glass and slab wood sections affixed into the assembly.
Instead, a 4′ x 9′ glass door was made with extreme capacity hardware. A magnificent slab of black walnut was peeled in half, and the inside face of each half was scored lengthwise in consecutive slots or “kerfs” that went 3/4″ through the 1″ thickness, leaving the outer faces virgin. These kerfs were then filled with structural silicone and the entire inner face of each slab was buttered with the silicone as well, and the two slabs were clamped together with the glass in between. The kerfing eliminated any “memory” and reaction stresses the slab might have introduced, in effect neutering it so it would act as a passive decorative skin.
The project grew aesthetically and technically, resulting in a visual tour de force that could not have been accomplished without these radical interventions.
The OneTree Project was born out of an extraordinary sequence of events…a meeting between Eric Poncon and John Houshmand in New York where they found their paths in a curious parallel (and a promise to “do something exciting together someday…”), the devastation of 3 million acres of forest lands in northeast Nicaragua’s indigenous frontier region (RAAN), Poncon’s appreciation for the work at JOHNHOUSHMAND, and our mutual love for great design, natural materials, and a philosophically sound interface with reality. And we do mean reality. Nothing unreal about sending a lawyer into the Nicaraguan frontier to search titles for 24,000 acres of small property holdings, negotiating fair purchase of these lands, obtaining IFC assistance, setting up extraction teams and a 12,000 board feet per day sawmill facility, reforestation programs and much, much, more…
Poncon, with architect and designer Matthew Falkiner (Morgan’s Rock eco-hotel, Simplamente Madera furniture company, and more…) invited Houshmand down to the frontier to see firsthand the devastation and the operations, and plan a series of joint ventures which will include projects such as: The “Handshake Collection” of extraordinary pieces designed and fabricated in our New York facilities using amazing wood elements from the immense salvage operation; the “Deep Roots Collection,” designed by Houshmand and Falkiner and made in Nicaragua comprising high design values, affordability, and increasing the training and viability of the local milling and artisan woodworkers; the “OneTree Collection,” a project to put pieces of two giant trees in the hands of 10 Nicaraguan and American artists respectively, and the works to travel as bonding collections. Another germinating concept is another eco-hotel with cabanas designed by guest architects/designers, each getting one tree for their creation. Other projects include value added use of the wood such as wall treatments, prefab housing, gluelam beams, countertops, even balsa surfboards… All FSC certified, all returning profits to reforestation, social, and educational projects, some of which are already falling into place. More to come! There is much more to come as well as an audio slideshow of my most recent trip to the jungles of Nicaragua.